The lifespan of a traditional pressure treated wood deck is about 10-15 years or less, depending on the durability of the materials, the way it was built, and its proper care. it requires pressure washing, sanding, staining, and sealing every 12 months. (Most wood decks are neglected).
Replacing the decking and railing with composite material (Trex, Timbertech) add 25 to 30 years to your neglected deck and up to 50 with capped polymer boards that could give 50 years or more of durability (Azek, Moisture Shield).
Do not take chances, the smart thing to do is to conduct a visual inspection of your deck by a licensed contractor, and NADRA certified Inspector who understand the governing codes that applies to deck construction. That is the very best way to detect defects before disaster strikes. Do not take chances with unlicensed or unexperienced contractors who give a very low price for a reason (A safe deck has much more components than an unsafe deck)
When inspecting your deck pay particular attention to better determine your options, in most cases if we have to replace more than 30% of the existing deck structure, it is highly recommended to replace it completely instead of just repairing it.
1. HOW IS THE PROCESS?
2. Improper attachment to the structure of the house – Ledger Board
How your deck attaches to your home determines its safety and durability. This is an area that you may want to overbuild beyond the minimum standards or requirements. The most common cause of total deck collapse involves the deck “pulling away” from a house. This type of failure typically occurs because the ledger board was not properly attached to the house.
The building code states the minimum distancing, patterns, fasteners and anchors
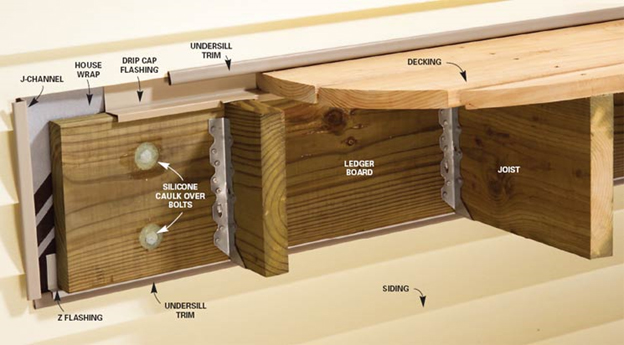
3. Improper or Missing Flashing
Every deck must address water management. Water can soak into your home at the point where the deck connects to the house. Properly installed flashing will prevent erosion to the structural integrity of your deck and home.
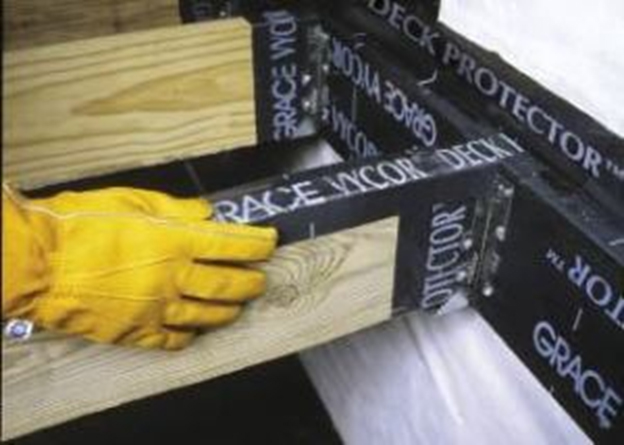
4. Undersized Footing – Damaged Post
Footings create a solid base for the posts of your deck. Undersized footings can lead to sagging, warping or collapse. Most decks have vertical wood posts that rest on top of concrete piers. Inspect the condition of the concrete to make sure it isn’t badly cracked or falling down.
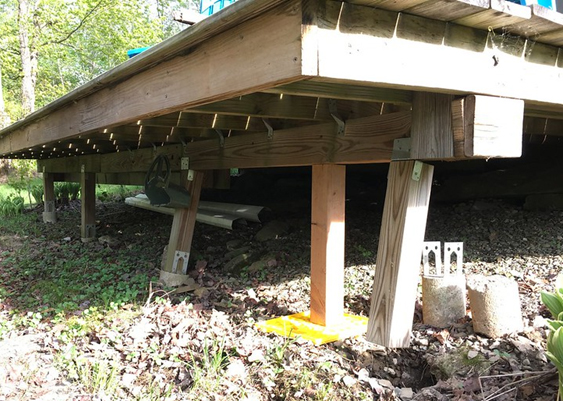
5. UNDERSIZED STRUCTURAL JOISTS & BEAMS
Don’t try to save money by skimping on undersized joists and beams—make sure everything is the right size for the job. Also, factor in the weight of occupants, snow and ice when you’re calculating how much weight your deck will bear. All decks have large horizontal beams resting on top of the support posts or piers. The beams, in turn, support all the floor joists. Therefore, the structural integrity of the entire deck is dependent upon the condition of the beams.
Check the beams for large cracks and water damage. Confirm that the beams are securely fastened to the tops of the posts or piers and that are not sagging under the weight of the deck. If it is, you’ll need to shore it up by installing one or more supports at mid-span.
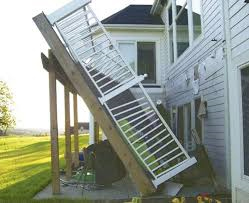
6. Missing or improper Joist Hangers and Corrosion Resistant treatments
Nails alone are not enough to counteract the shear forces on a structural member. Joist hangers are an essential element in creating reinforced connections and supported decking. As mentioned earlier, the ledger board and beams support all the floor joists, which are usually spaced 16 in. on-center. The ends of the joists often sit in metal joist hangers. Be sure that each hanger is firmly fastened in place with hanger nails, not screws or common nails.
Ensure the safety of your deck by using properly sized, engineered, and correctly installed joist hangers. Weather-resistant materials are necessary on exterior structures to prevent rot or deterioration. There are specific fasteners for certain wood treatments and it is critical that the proper fasteners are used. Select materials that are expressly made to withstand all weather conditions.
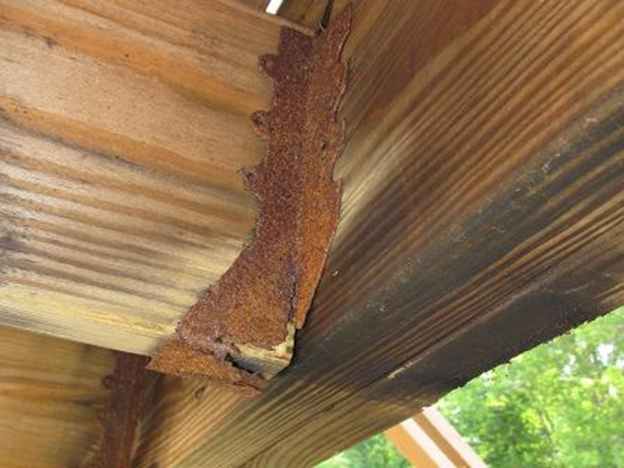
7. Improper Railing height and baluster spacing
Building codes have very specific measurements for railings and balusters to avoid accidents and injuries. Decks higher than 30 in. above the ground should have a perimeter railing. And it’s critically important that railings be kept in good, sound condition, and here’s why: Although catastrophic deck collapses always make the nightly news, a vast majority of deck injuries are caused by someone leaning against, and breaking through, a defective railing.
Start by confirming that each railing post is firmly attached to the deck frame and is free of large cracks, rot or insect damage. Railing posts should be fastened with lag screws or carriage bolts, not nails or decking screws. And if the bottoms of the posts are notched around the rim joist, check to be sure the posts aren’t splitting at the notches.
Each vertical baluster must be secured fastened to the horizontal rails. They must also be in sound condition and spaced no more than 4 in. apart. The handrail should be free of rough spots and splinters.
Measure the height of the guardrail from the decking to the top of the handrail. It should be at least 36 in. high, although some towns require 42-in.-high deck railings. Check with the local building department for the correct railing height in your town.
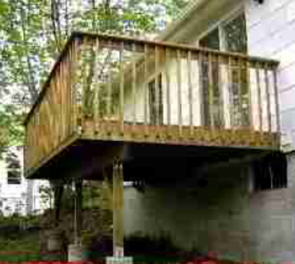
8. Unsafe Stairs – Open Risers – Posts
If your deck has a staircase or set of steps, you must check each component—treads, stringers, handrails, balusters, support posts—for signs of structural damage, including large cracks, loose connections, and missing fasteners.

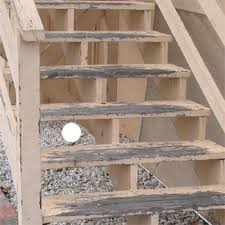
9. Unsealed Deck
Wood that is unsealed can get weathered and deteriorate much faster than sealed decks. Not only do unsealed decks look worn out and old, but it can also shorten the lifespan of your deck.
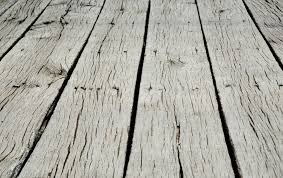
10. Diagonal Bracing – Lateral Load Provision
Most tall decks have diagonal bracing angling up from the support posts to the deck frame. The braces help stabilize the deck and deter it from swaying back and forth. Inspect each brace for large cracks or rot, especially at the ends. Replace all damaged braces. Then, confirm that each brace is securely fastened with lag screws.
Let’s say you own a house with a finished basement and no deck. Let’s say you’d like to add a deck by attaching it to your house using a ledger board. Well, depending on where you live, your job may have just gotten significantly more difficult.
Changes to International Residential Code for projects where decks are supported by an adjacent structure (your house), now require a “positive attachment” to resist lateral loads. That positive attachment is a new piece of hardware called a hold-down device “with an allowable stress design capacity of not less than 1,500 pounds”, which must be installed on at least two locations per deck (IRC 2012 Section R507.2.3).
These new hold-down devices must be attached to the joists of the deck, penetrate through the ledger board, the wall sheathing and band joist of the house, and then fasten to the floor framing inside the house
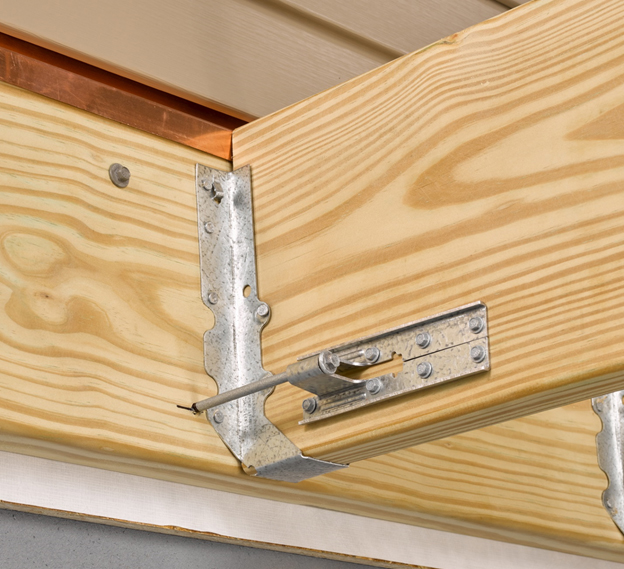
Are you ready for a Deck Inspection?
Please fill out the form by clicking on https://e81studio.com/contact
Rafael Antonio Huguet Lotterer, Owner of E81 Studio
Certified by NADRA (National Association of Deck and Railing) Inspector
Call us: (240) 205-3758
Or E-mail us at: info@e81studio.com
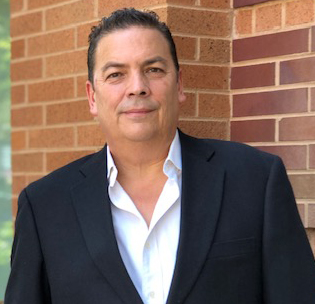